Die Casting Automotive: Revolutionizing Metal Fabrication in the Auto Industry
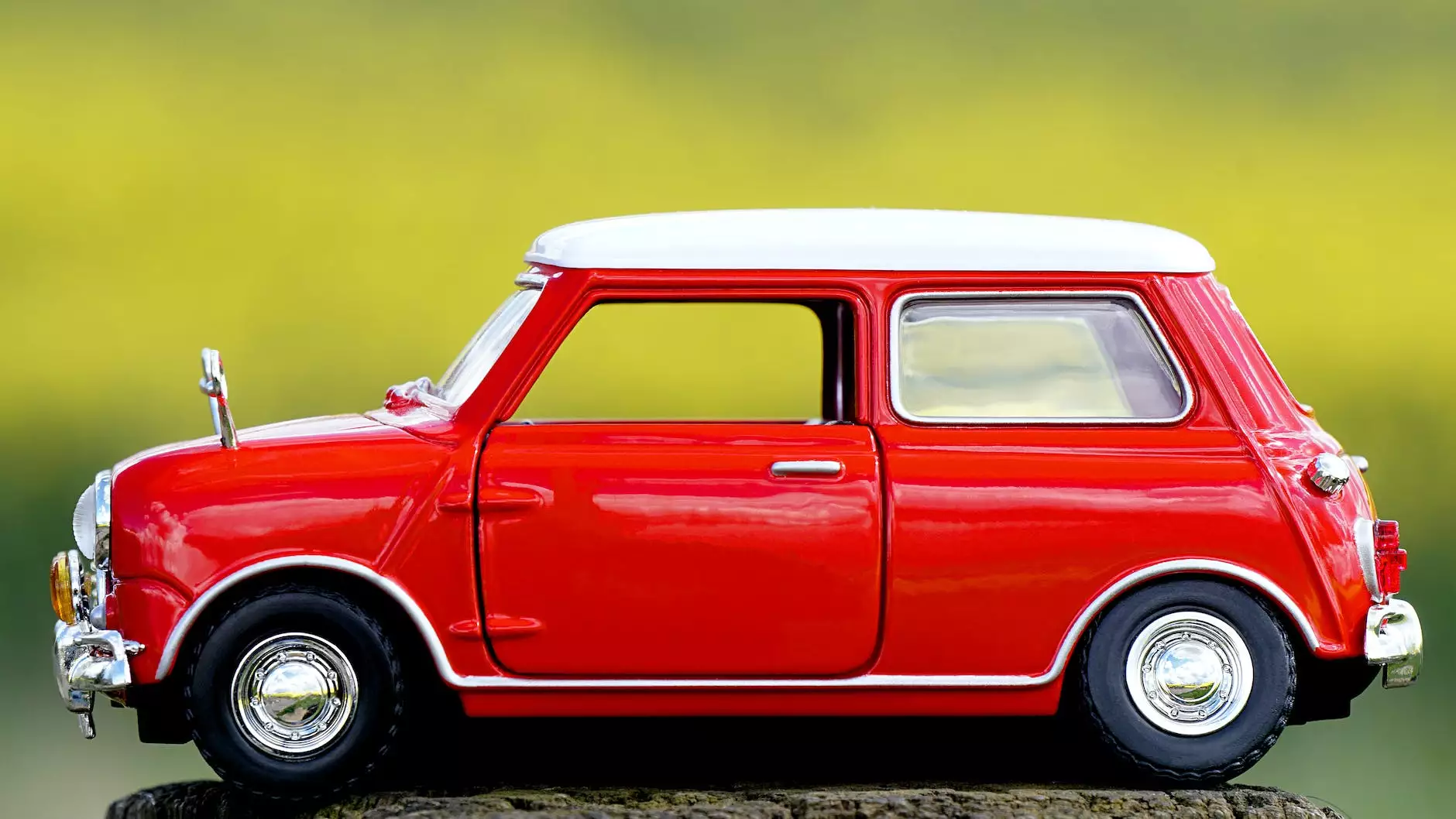
The Importance of Die Casting in the Automotive Sector
In the world of automotive manufacturing, die casting automotive has emerged as a cornerstone technique that enhances efficiency, precision, and quality. This process involves pouring molten metal into a mold to form specific shapes, making it ideal for creating components with intricate designs and exceptional strength. The ability to produce complex geometries at a lower cost and with shorter lead times has made die casting a popular choice among manufacturers.
Understanding the Die Casting Process
The die casting process demystified involves several critical steps:
- Preparation: The first stage includes preparing the die, which is specifically designed to create the desired shape of the automotive part. The die is typically made from steel to withstand the high temperatures and pressures involved.
- Melting: The metal, commonly aluminum or zinc, is heated until it reaches a molten state. This melting process is crucial as it impacts the flow characteristics and final properties of the cast part.
- Injection: In this step, the molten metal is injected into the prepared mold at high pressure. The rapid injection process ensures that the metal fills every crevice and detail in the die.
- Cooling: Once the mold is filled, the metal begins to cool. This solidification phase is essential, as it directly affects the mechanical properties of the final product.
- Ejection: After sufficient cooling, the die is opened, and the casting is ejected. The process allows for high-volume production, making it efficient for automotive components.
Advantages of Die Casting in Automotive Manufacturing
There are numerous advantages to using die casting automotive techniques, including:
- Precision and Accuracy: Die casting produces parts with tight tolerances, which is crucial for the automotive industry where precision is often paramount.
- Cost-Effectiveness: While the initial setup costs may be high, the long-term savings in production runs make die casting a cost-effective solution for mass production.
- Complex Shapes: The technique allows for the creation of complex geometries that might be impossible with other manufacturing methods.
- Material Efficiency: Die casting minimizes waste material, leading to a more sustainable manufacturing process.
- Enhanced Mechanical Properties: The process results in castings with improved strength and durability, essential for components subject to high stress and strain.
Applications of Die Casting in the Automotive Industry
The automotive industry leverages die casting technology in several areas, including but not limited to:
- Engine Components: Critical parts such as oil pans, engine blocks, and cylinder heads are often manufactured using die casting.
- Transmission Housings: The lightweight yet sturdy nature of die-cast aluminum makes it ideal for transmission cases.
- Chassis and Suspension Parts: Components like control arms and brackets benefit from the strength and precision die casting offers.
- Interior Components: Die casting is also utilized for aesthetic features and functional parts within the vehicle’s interior.
Quality Control in Die Casting
Ensuring quality in die casting automotive applications is paramount. High-quality parts lead to improved performance and safety. Here are some methods used to maintain quality:
- In-Process Testing: Quality checks during the casting process can identify defects early, allowing for immediate corrective measures.
- Visual Inspections: Finished parts undergo thorough visual inspections to ensure they meet the required standards.
- Mechanical Property Testing: Tests that measure the strength, ductility, and fatigue limits of the parts are regularly conducted.
The Future of Die Casting in Automotive Manufacturing
The die casting automotive industry is poised for significant advancements as technology continues to evolve. Innovations such as:
- 3D Printing of Molds: This emerging technology can reduce the time and cost associated with creating complex molds, enabling faster market responsiveness.
- Smart Manufacturing: The integration of IoT (Internet of Things) in die casting processes will enhance monitoring and data collection, leading to improved process control and efficiency.
- Advanced Alloys: Research into new, lightweight alloys will allow for the production of even stronger and more efficient automotive components.
Conclusion
In conclusion, the significance of die casting automotive in shaping the future of the automotive industry cannot be overstated. Its ability to produce high-quality, precise, and complex parts makes it an indispensable process for manufacturers aiming for excellence in the ever-competitive auto market. As die casting technology continues to evolve, it will undoubtedly play an even more critical role in driving innovation and sustainability within the industry.
For further insights into die casting and its impact on automotive manufacturing, explore the offerings at deepmould.net. Discover high-quality metal fabricators dedicated to pushing the boundaries of engineering excellence in production.