High Pressure Die Casting Manufacturers: The Future of Metal Fabrication
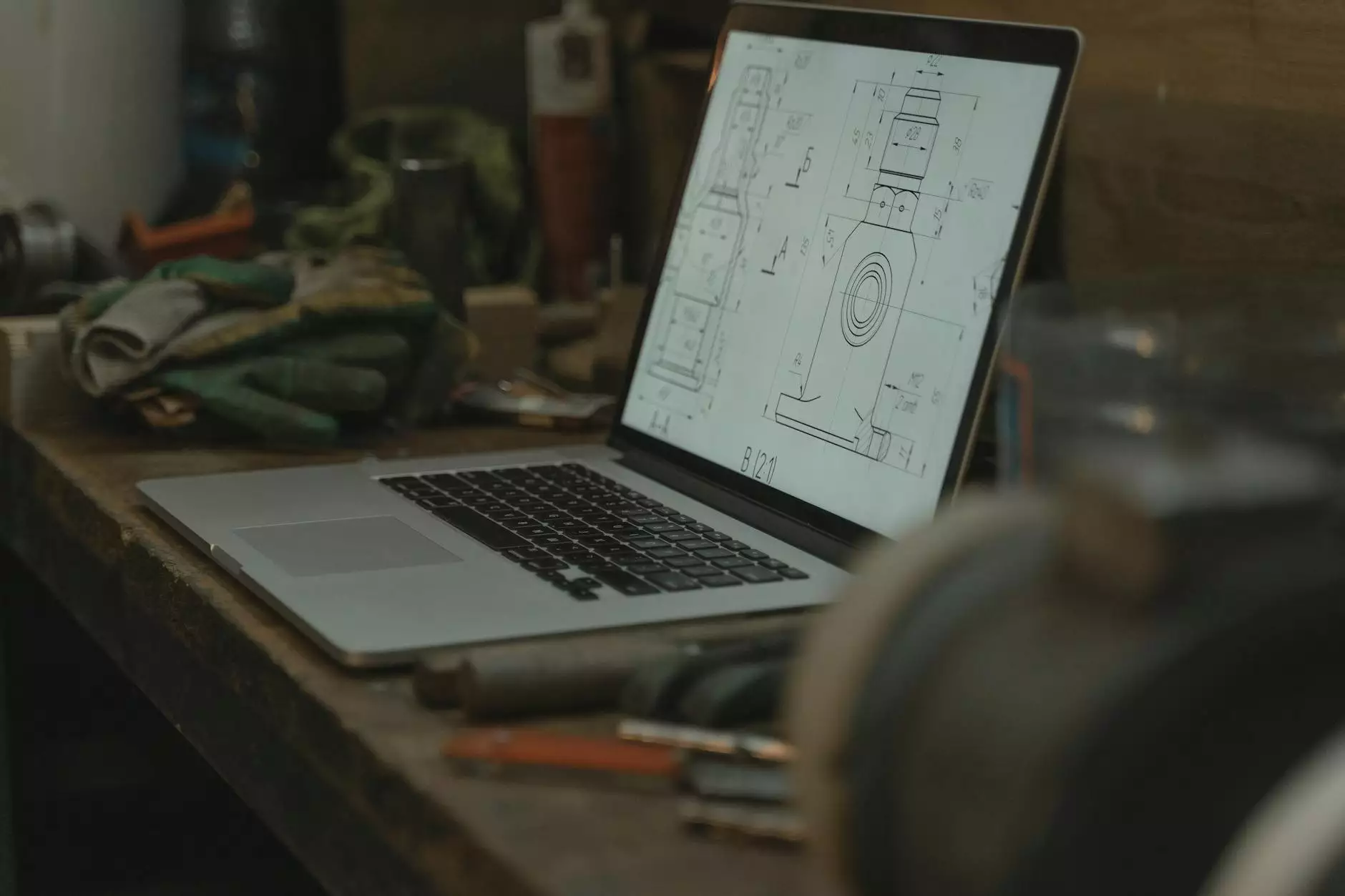
High pressure die casting manufacturers play a pivotal role in the realm of metal fabrication, providing superior manufacturing solutions that dramatically enhance production efficiency and product quality. As industries evolve, the demand for precision-engineered components and advanced metal forming techniques has never been higher. This comprehensive article delves into the intricate world of high pressure die casting, highlighting its benefits, applications, and how it stands as a cornerstone for numerous sectors.
Understanding High Pressure Die Casting
At its core, high pressure die casting is a process where molten metal is injected into a mold under high pressure. This method allows for the creation of complex shapes with excellent surface finish and dimensional accuracy. The molten metal, typically aluminum, zinc, or magnesium alloys, is forced into a metal mold through a nozzle. Once cooled, the mold is opened and the cast part is ejected.
Key Features of High Pressure Die Casting
- High Speed Production: One of the most significant benefits is the ability to produce components rapidly, making it ideal for large-scale manufacturing.
- Excellent Surface Finish: The process yields components with a superior surface finish, often requiring little to no additional machining.
- Dimensional Stability: High pressure die casting allows for high precision and repeatability, essential for industries requiring tight tolerances.
- Design Flexibility: Manufacturers can create intricate and complex shapes that would be challenging to achieve with other methods.
The Advantages of High Pressure Die Casting
High pressure die casting offers numerous advantages that appeal to manufacturers across a spectrum of industries. Here are some of the standout benefits:
1. Cost Efficiency
Although the initial tooling costs may be higher compared to other casting methods, the long-term benefits of high pressure die casting—such as reduced machining and finishing costs—lead to significant overall savings. The rapid production capabilities also decrease labor costs.
2. Lightweight Components
By using alloys like aluminum, high pressure die casting allows manufacturers to produce lightweight components without compromising strength. This is particularly beneficial in industries like automotive and aerospace, where weight reduction translates to improved fuel efficiency.
3. Environmentally Friendly
High pressure die casting manufacturers are increasingly adopting sustainable practices. The use of recyclable materials, coupled with efficient production processes, minimizes waste and reduces the ecological footprint. Moreover, the accuracy of the die casting process means less metal is required overall.
Applications of High Pressure Die Casting
The versatility of high pressure die casting makes it suitable for a variety of applications across multiple industries. Some notable applications include:
Automotive Industry
In the automotive sector, high pressure die casting is pivotal for producing parts such as gearboxes, electric motor housings, and various brackets. The process allows for creating complex geometries essential for modern automotive designs.
Aerospace
The aerospace industry benefits from high pressure die casting for components that require stringent quality standards and lightweight materials. Parts like structural elements and engine components are often manufactured using this method.
Electronics
High pressure die casting is utilized in the electronics sector for enclosures and structural components. The excellent finish and intricate designs achievable through this process cater to the high aesthetic and functional demands in electronics.
Choosing the Right High Pressure Die Casting Manufacturer
With multiple high pressure die casting manufacturers in the market, selecting the right partner can significantly impact your production process. Here are some key factors to consider:
1. Experience and Expertise
Look for manufacturers with a proven track record in high pressure die casting, particularly in your industry. Their experience often translates to better quality, more efficient processes, and innovative solutions.
2. Technology and Equipment
Advanced technology and up-to-date machinery are crucial for high quality outputs. Manufacturers that invest in state-of-the-art equipment will typically produce components with greater precision and efficiency.
3. Quality Assurance Processes
High pressure die casting requires stringent quality controls to ensure that every component meets industry standards. Inquire about the quality assurance practices employed by potential manufacturers.
The Future of High Pressure Die Casting
The future of high pressure die casting looks promising, with continuous advancements in technology and processes. Key trends shaping the future include:
1. Automation and Industry 4.0
Incorporating automation into die casting processes enhances productivity and consistency. The integration of IoT for real-time monitoring and data analysis is transforming how manufacturers operate, leading to increased efficiency and reduced downtime.
2. Research and Development
Manufacturers are investing heavily in R&D to develop new alloys and improve die casting processes. These advancements lead to even lighter components with better performance characteristics.
3. Sustainability Initiatives
As industries shift towards greener practices, high pressure die casting manufacturers are focusing on sustainability. From using recycled materials to minimizing energy consumption, the push for a lower environmental impact is driving innovation in the sector.
Conclusion
High pressure die casting manufacturers are at the forefront of metal fabrication innovation, providing solutions that significantly enhance production efficiency and product quality. With a plethora of advantages, including cost-efficiency, lightweight components, and environmentally friendly practices, the adoption of this manufacturing process is on the rise across diverse industries. Selecting the right manufacturer is integral to leveraging these benefits, and understanding the trends that will shape the future of high pressure die casting will prepare businesses for the next generation of manufacturing excellence.
For businesses looking to procure high quality die cast components, consider partnering with reputable manufacturers such as those found at deepmould.net, who excel in delivering comprehensive die casting solutions tailored to diverse industrial needs.